RET TECHNOLOGIES TRANSFORM RECYCLING
The process developed by RET offers a revolutionary technological basis for the mechanical recycling of lithium-ion batteries. Building on many years of experience in plant engineering, our systems enable efficient, safe and scalable processes – for the clean recovery of black mass and other valuable materials.
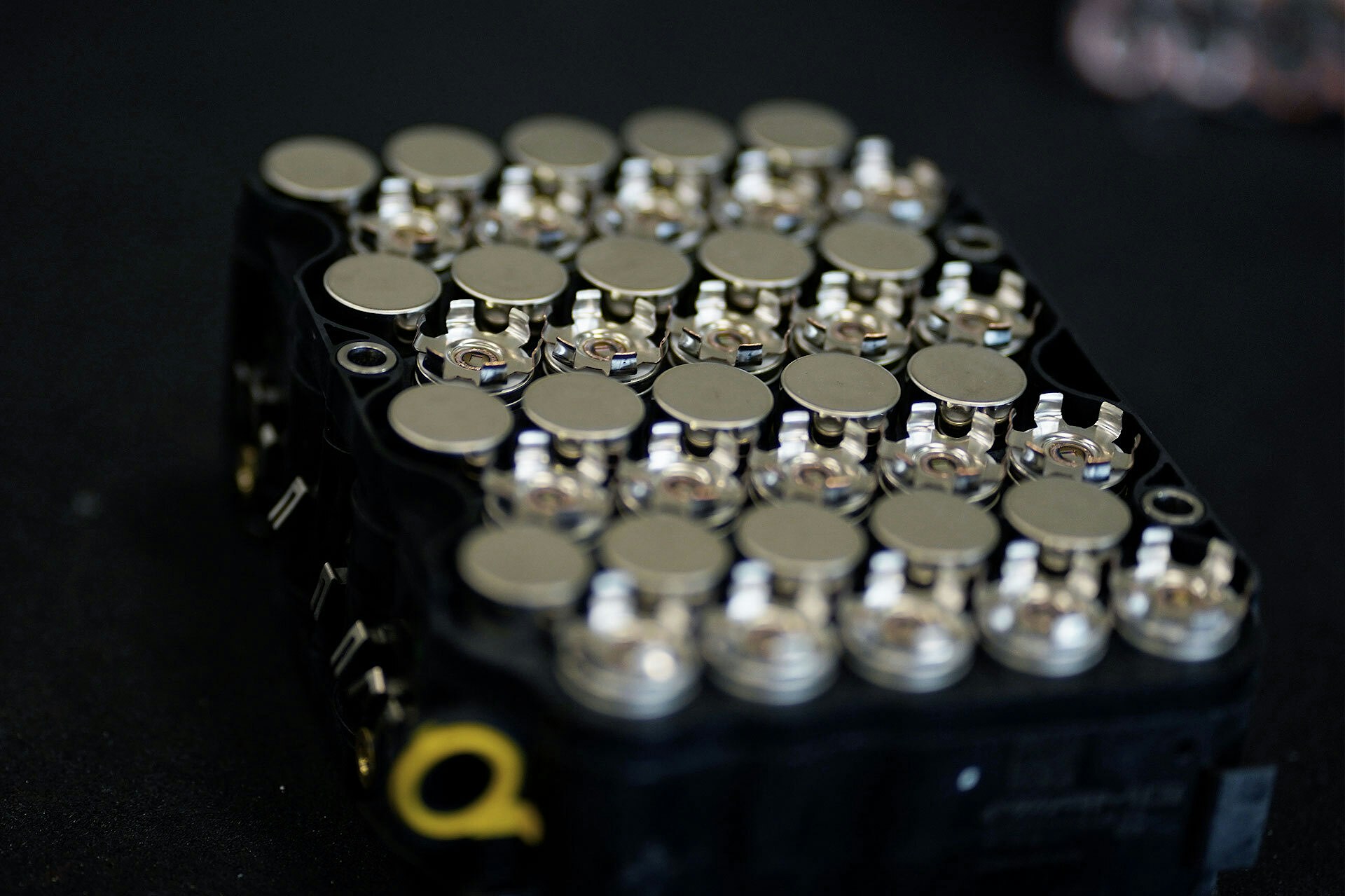
THE BATTERY CHALLENGE
Thinking about tomorrow today!
We are well aware of the challenge that the coming years will bring.
The production and marketing of lithium-ion batteries (LIB) is steadily increasing. The electromobility sector alone is growing exponentially. Additionally there’s all the consumer batteries that can be found in smartphones and other electronic devices, for example. From today’s perspective, the amount of used batteries returned in Europe will increase eightfold by 2030. By 2040, 40 times as many used batteries will probably need to be recycled. This is why we want to make a significant contribution to establishing a circular economy for used batteries and thus conserve our planet’s limited resources.
Our Performance
By using our impact reactor, our customers achieve very high black mass yields and purity – even with challenging cell types.
Our technology already meets the technical requirements for tomorrow’s legal quotas – proven in practice and scalable.
The high purity of the black mass recovered enables efficient further processing in the hydrometallurgical process.
Our plant solutions are not only economical, but also resource-efficient and safe to operate.
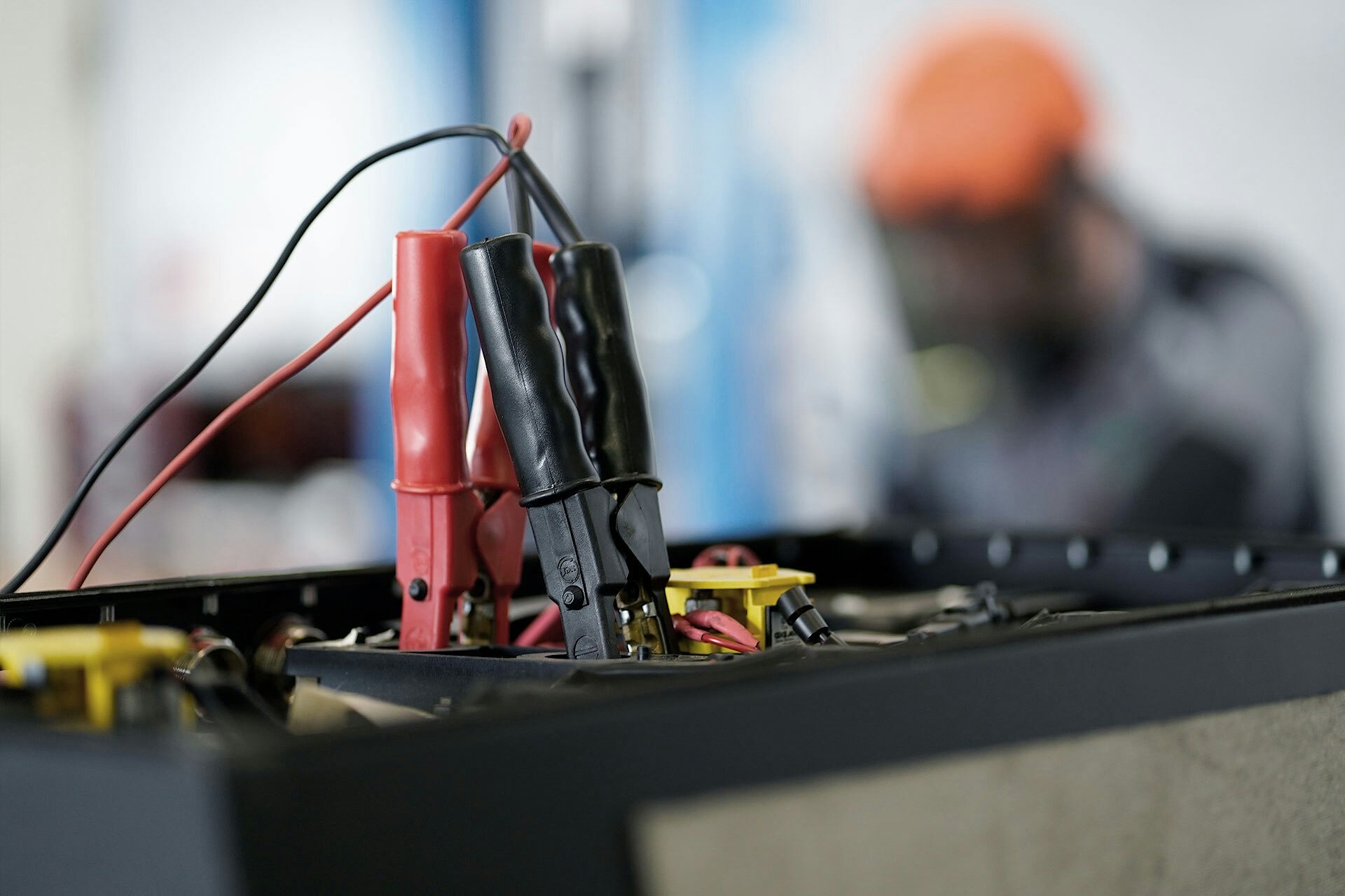
The RET process for recyclers: Discharge
Unloading - efficient, clean and safe
To ensure maximum process and work safety, the batteries are deeply discharged to 0 V. It doesn’t matter whether it’s entire packs, modules or individual cells.
The controlled discharge of the residual electrical energy still stored in the cells reduces the risk potential for the subsequent recycling process. The energy demand for the entire process is reduced, since the stored energy is fed back into the grid.
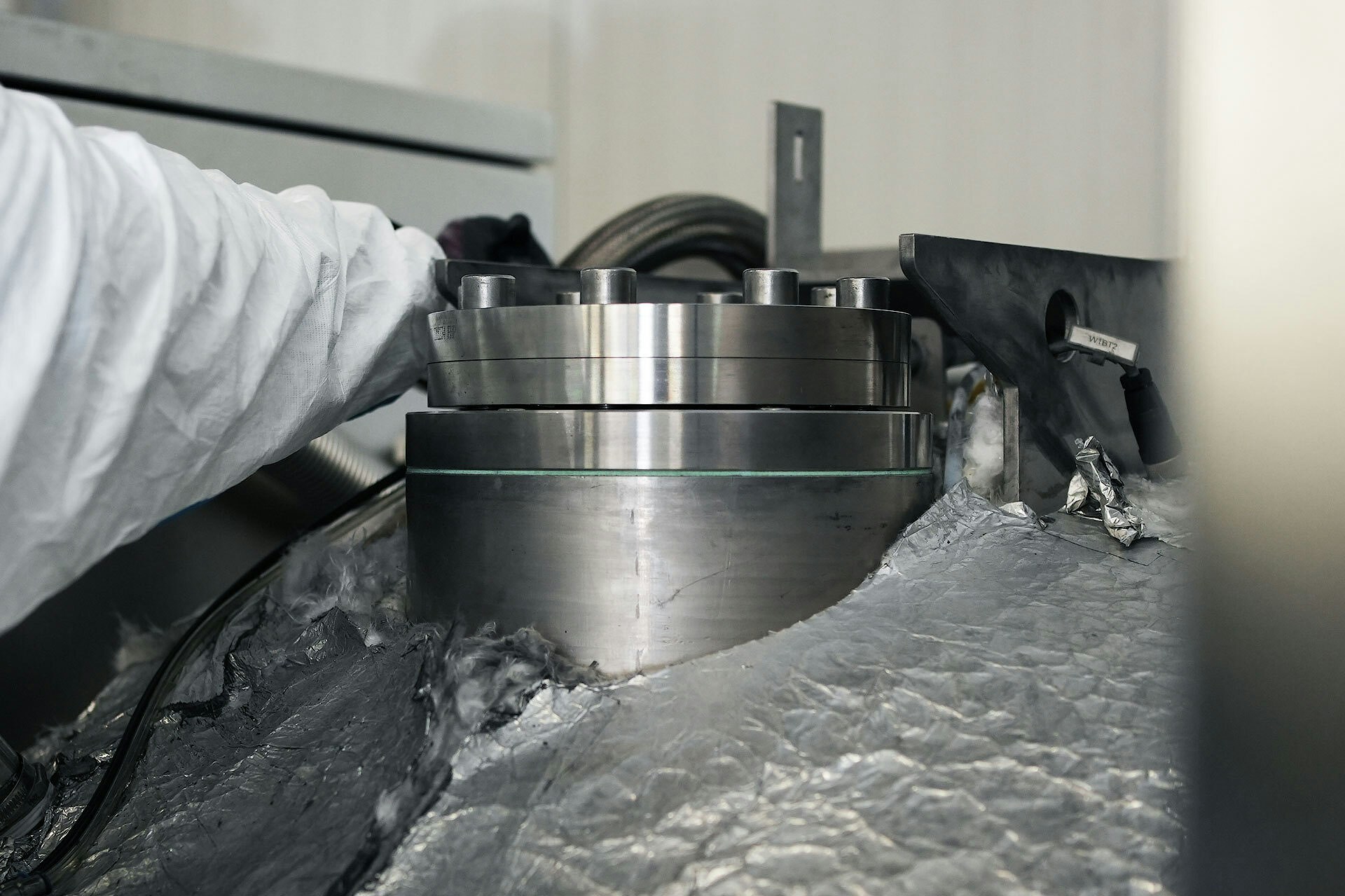
The RET process for recyclers: DRYING
Drying - innovative, precise and customizable
Depending on the size of the system, the batteries are safely preshredded either in an inert atmosphere or in a vacuum. The electrolyte is separated and recovered in a highly effective dryer specially developed for this application.
The discharged lithium-ion batteries are shredded in an inert atmosphere and thus broken down. The battery components are then fed into our vacuum drying process, in which the volatile electrolytes evaporate by means of heat and vacuum. These are then condensed out again and bottled in liquid form. Only the dried cell components are then sent for mechanical separation.
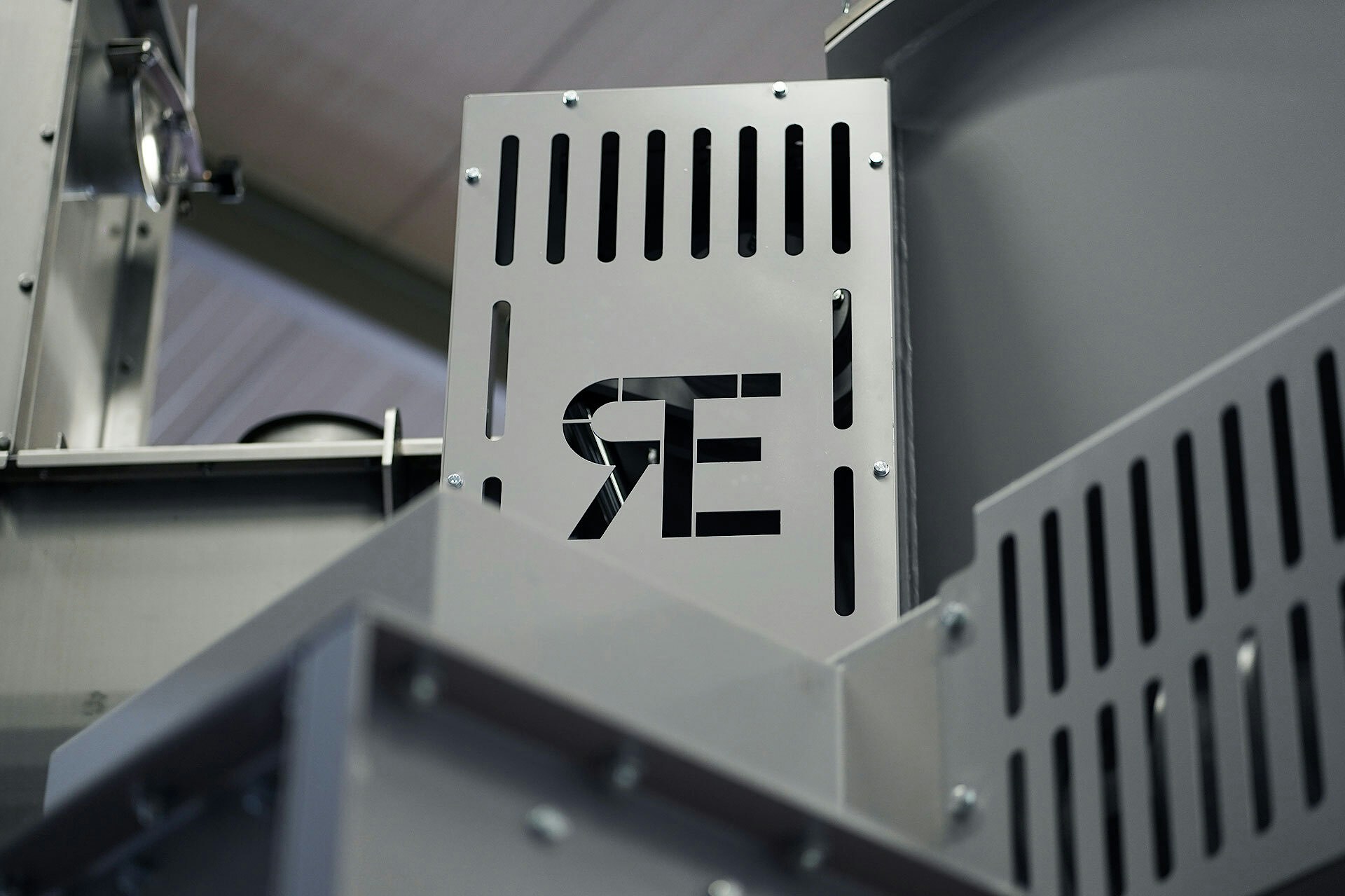
The RET process for recyclers: SEPARATION
Impact reactor - high-quality, effective and powerful
Only one unit is required for delamination of the electrode foils, for the spherification of metals and for separation of the black mass: The RET impact reactor.
By using the impact reactor, we guarantee a high yield and yet very clean black mass, even with previously untreated, dry production scrap. The dry cell components are fed into the impact reactor. A special rotor ensures that the coatings are detached from the metal foils and the released Black Mass is discharged using an air flow and patented deflector wheel technology. Meanwhile, the housing parts, separators and metal foils are spherified and then separated from each other by suitable separation units and bagged as pure fractions.
Our Technologies
Revolution in battery recycling
From discharging and drying to separation in the impact reactor. All current lithium-ion batteries can be recycled safely and effectively in an efficient, clean process using state-of-the-art technologies.
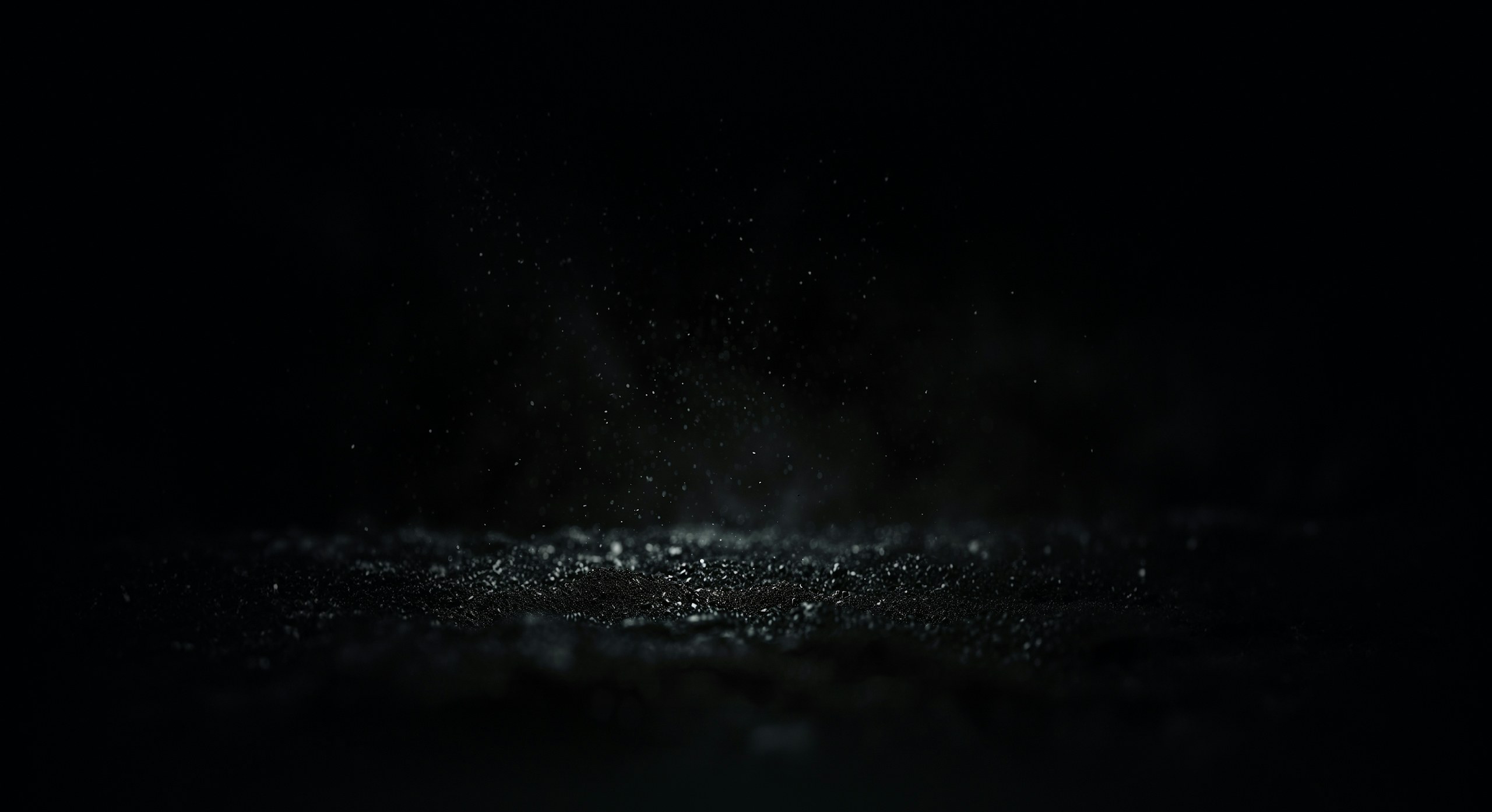
SUSTAINABLE CAREER PLANNED?
Apply with us!
Our job offerings not only provide you with a secure future perspective but also the opportunity to actively contribute to shaping a sustainable future.
With us, you’ll find jobs that not only advance your career but also your values. Join a movement that will change the world and start your sustainable career with us today!