EFFICIENT VACUUM DRYING FOR LITHIUM-ION BATTERIES
Discover our environmentally friendly and safe method for vacuum drying lithium-ion batteries that redefines quality and efficiency in the recycling process.
PIONEERING DRYING TECHNOLOGY: THE RET VACUUM DRYER
No drying, no flammable electrolyte
Create the ideal basis for the best black mass quality with the low-emission recovery of electrolytes.
Reckelberg’s vacuum drying technology offers a pioneering solution that not only improves the safety and environmental compatibility of your recycling process, but also makes a significant contribution to cost efficiency and material recovery. By integrating our innovative drying into your operations, you can maximize the reuse of valuable raw materials while strengthening your market position.
Highlights
Safe and low-emission recovery of volatile organic electrolytes
Low temperatures in the vacuum dryer ensure high-quality black mass
The drying process drastically reduces the fire risk of the batteries
More efficient processing and material recovery, e.g. through parallel redundant drying
EFFICIENT INERTING AND GRAIN SIZE OPTIMIZATION
Lithium-ion batteries require careful drying after discharge in order to effectively isolate the flammable electrolyte. At Reckelberg Environmental Technologies, we offer modern vacuum dryers for a tried and tested process. The batteries to be processed can be inerted through an advanced airlock system. Subsequently, a four-shaft rotor shear ensures an optimal grain size and thus guarantees the quality of the recycling process.
In the next phase, our RET vacuum dryers are used. These double-walled horizontal paddle dryers are designed to efficiently vaporize the volatile organic battery electrolytes. Thanks to the high-performance vacuum system, drying takes place at low temperatures, which increases the safety of the process and improves the quality of the end product.
SUSTAINABLE RECOVERY AND EMISSION CONTROL
As the process continues, the dryer collects and condenses the vaporized electrolytes using an innovative multi-stage heat exchanger system. This process enables the electrolytes to be efficiently collected and bottled in liquid form, allowing the valuable resource to be recovered and returned to the circular economy.
Finally, our sophisticated exhaust air purification system ensures that emissions remain consistently below the strict EU limits. In addition, the system automatically optimizes the dwell time and the drying process to achieve an ideal result with minimized inert gas consumption. Once drying is complete, the cell components are ideally prepared for further processing.
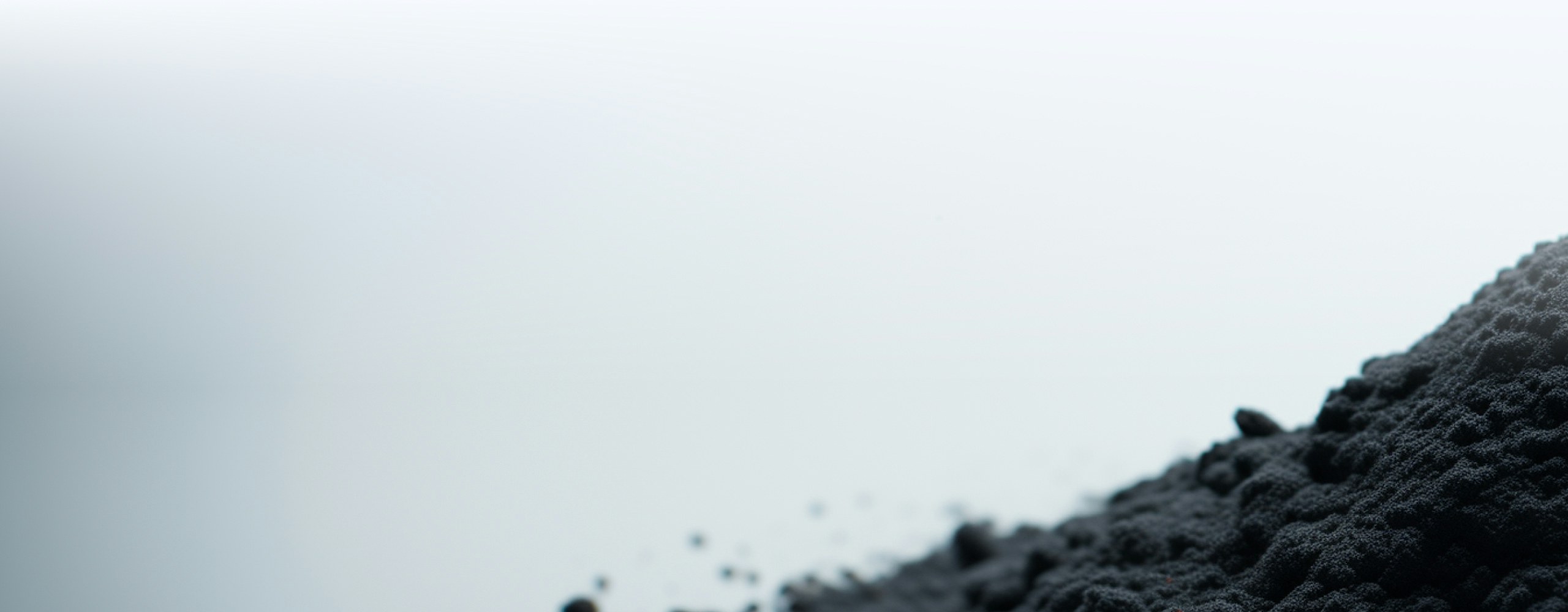
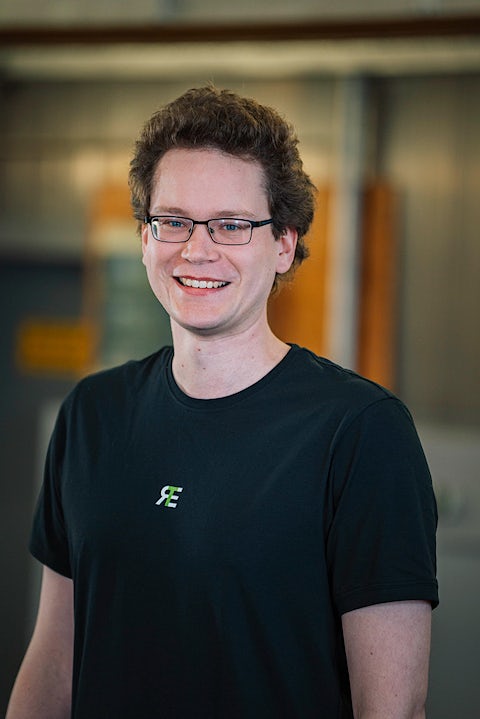
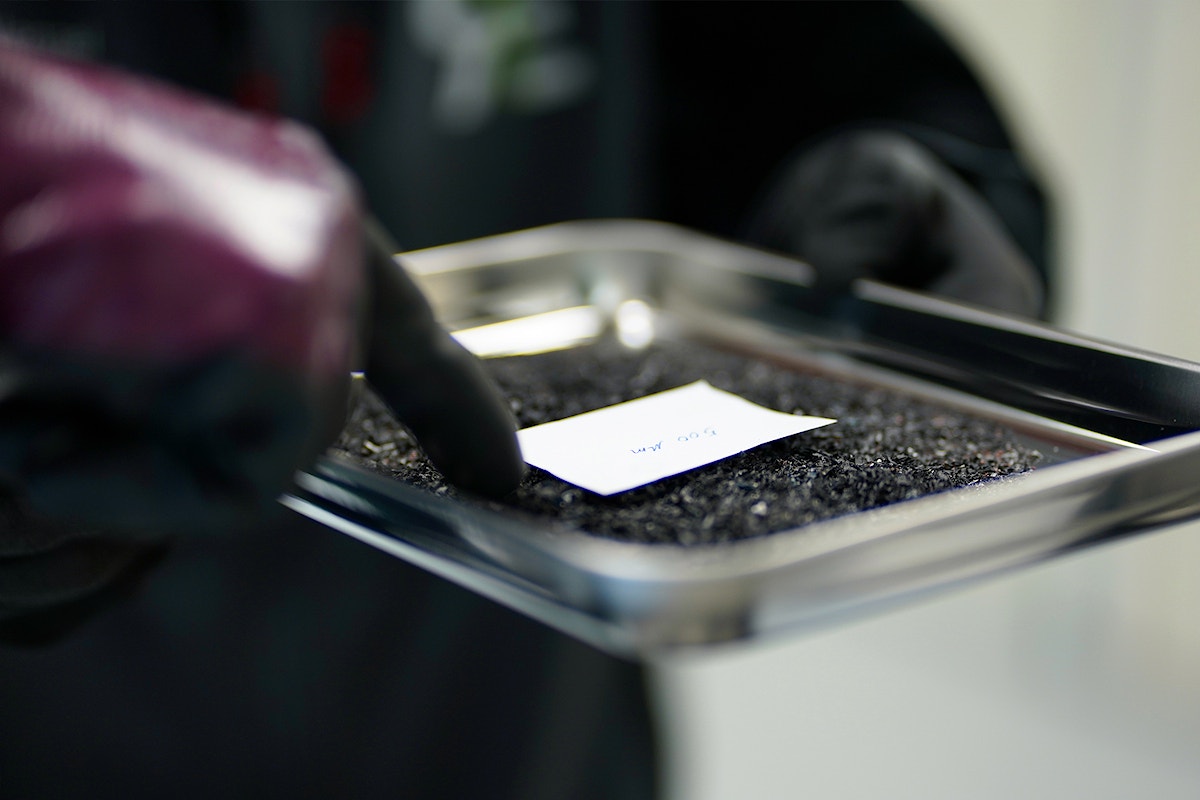
ENTRY INTO ELECTROLYTE RECOVERY
What the vacuum dryer does in practice
A recycling operator based in Eastern Europe has decided to use RET vacuum drying to remove the electrolytes contained in previously shredded battery material from discharged and dismantled lithium-ion batteries, thus ensuring safe processing in mechanical treatment.
Facts about the project
>96% electrolyte recovery with a standard market composition
Uniform drying of the cell components and parallel redundant drying
Gentle heating for best black mass quality
Drastic reduction of the fire load
Other Technologies
Revolution in battery recycling
From discharging and drying to separation in the impact reactor. All current lithium-ion batteries can be recycled safely and effectively in an efficient, clean process using state-of-the-art technologies.