IMPACT REACTOR: LEADING THE WAY IN BATTERY RECYCLING
With our patented impact reactor system, we are revolutionising the technology behind effective battery recycling processes. Discover one of the world’s most innovative technologies for recovering black mass with the highest output quality.
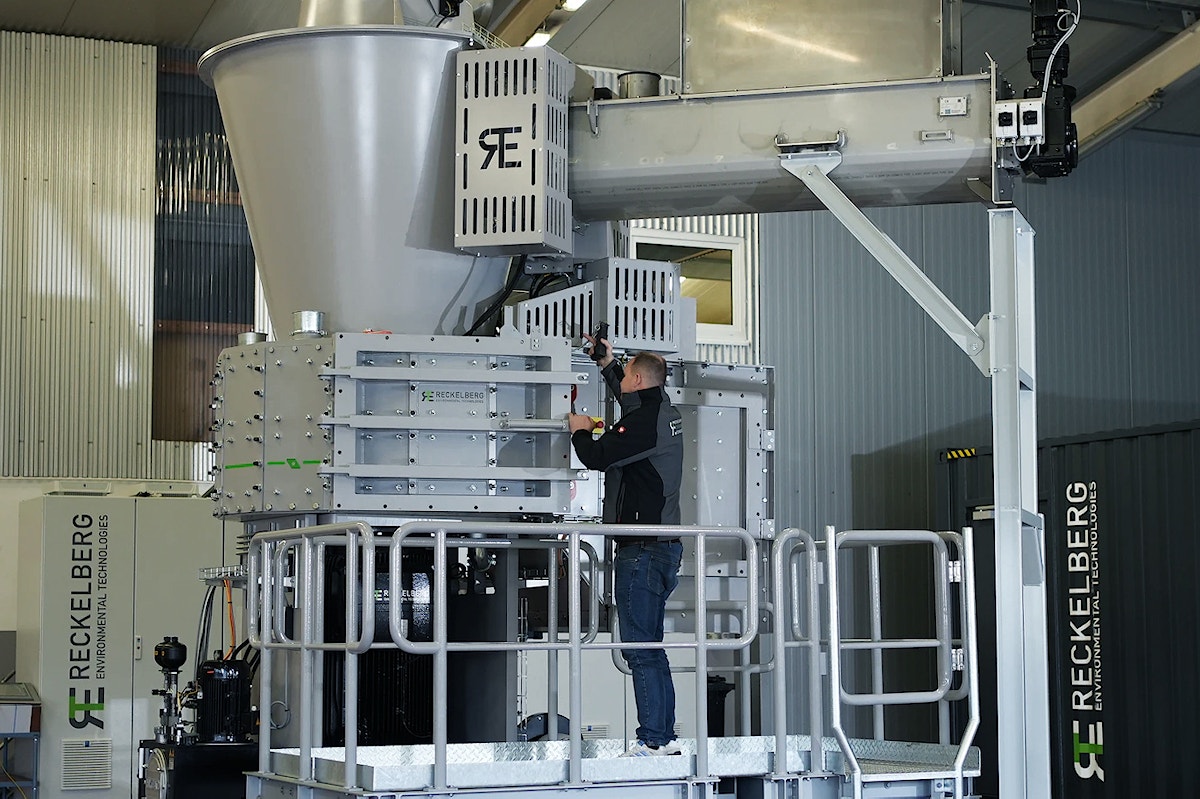
MECHANICAL SEPARATION OF RAW MATERIALS
The key to the battery recycling revolution
For the highest output qualities, regardless of the input material.
Reckelberg Environmental Technologies is revolutionizing battery recycling with the impact reactor, a pioneering technology that offers first-class efficiency and sustainability. The impact reactor impresses with its ability to precisely separate battery components and effectively recover valuable metals. It is characterized by high material purity and yield and is also robust against impurities. For companies that value quality, efficiency and sustainability, the impact reactor offers an unrivaled solution in battery recycling.
Highlights
Highest purity and quality of the recovered Black Mass
Highest yield of valuable metal fractions
Integrated separation of powdery hazardous substances and robust design
Particularly insensitive to interfering substances due to the geometry of the impact reactor
PRECISE MECHANICS IN THE IMPACT CHAMBER
The impact reactor from Reckelberg Environmental Technologies uses advanced mechanical process technology - specially developed for battery recycling. The effective separation of metals and black mass in the impact chamber, supported by highly wear-resistant impact elements, is a key advantage of this technology. Specifically, a special rotor accelerates the material against the walls, which leads to decomposition by utilizing the impact energy of the material against each other and against the highly wear-resistant lining of the impact chamber. This frees heavy housing parts (steel and aluminum) and electrode material (aluminum and copper) from the black mass and largely ensures that they are spherefied.
OPTIMIZED AIR FLOW FOR MAXIMUM SEPARATION
An innovative airflow system in the impact reactor contributes to the precise separation of materials. The decoating of the Metal Foils takes place within the first few seconds and a strong air flow removes the released black mass directly from the impact chamber. This ensures that no Black Mass is encapsulated inside the metal spheres. This air flow is generated by the movement of the rotor, and specially developed purge and suction-air system to transport the black mass upwards. Due to its low weight, it also captures separator foils and smaller aluminum and copper particles. To remove these foils and metals from the black mass, the impact reactor has deflector wheels. The appropriate geometry and rotational speed of these deflector wheels ensure precise separation between the dusty black mass and the “impurities”. This guarantees the high purity and quality of the recovered Black Mass.
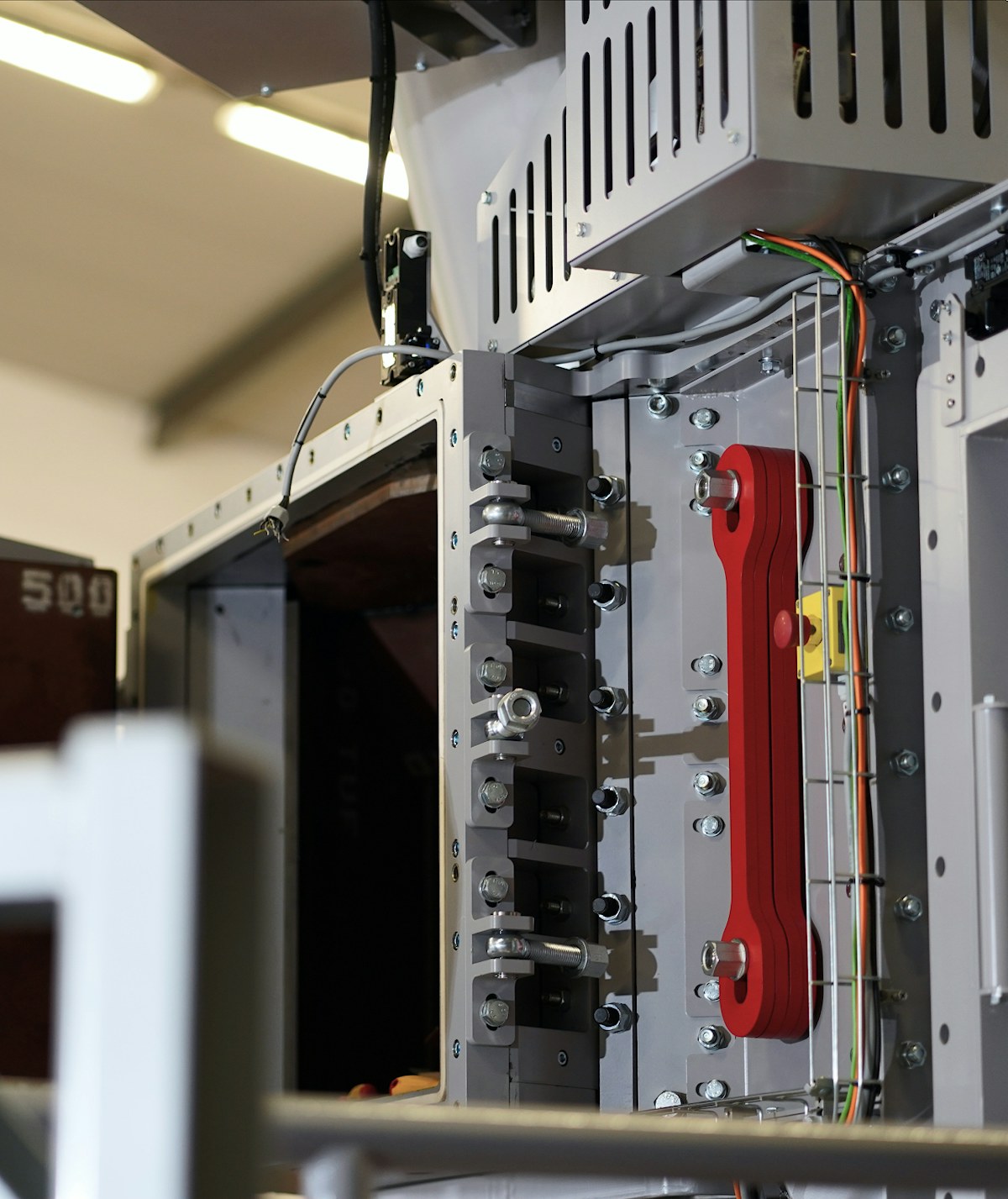
FOCUS ON EFFICIENCY AND SUSTAINABILITY
The entire process takes place in batches. At the end of each batch, the remaining coarse material, which is now free from Black Mass, is ejected via the discharge flap and can then be separated further. Batch processing in the impact reactor enables quasi-continuous and very efficient material separation. With its patented system and class-leading performance, the impact reactor guarantees efficiency in the recycling process. In addition to the recycling of batteries, it is also suitable for a wide variety of tough separation tasks in recycling such as CFRP processing (separation of carbon fibers from the matrix), the decoating of painted wood and the separation of plastic (PE) / tinplate / paint and many more.
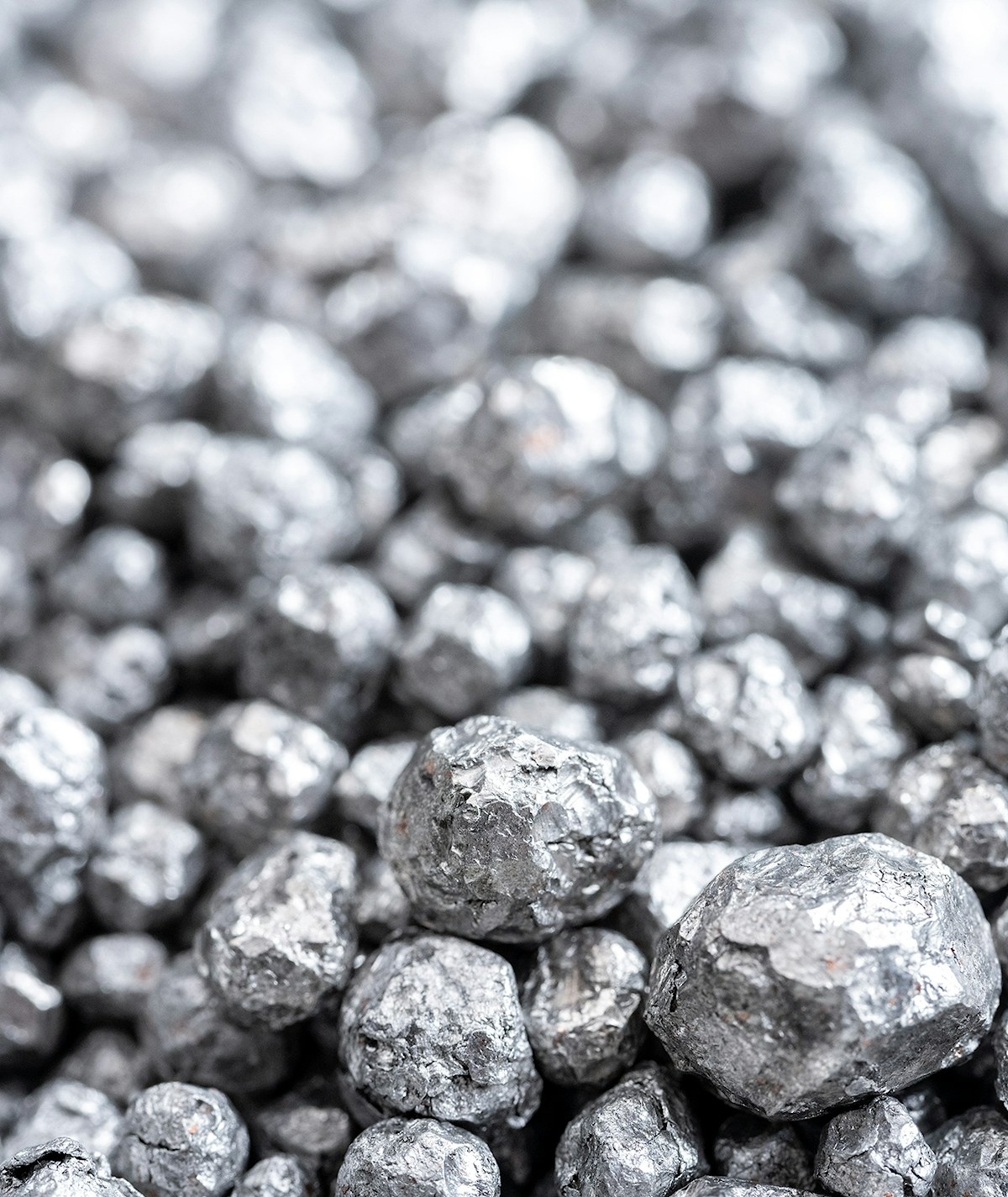
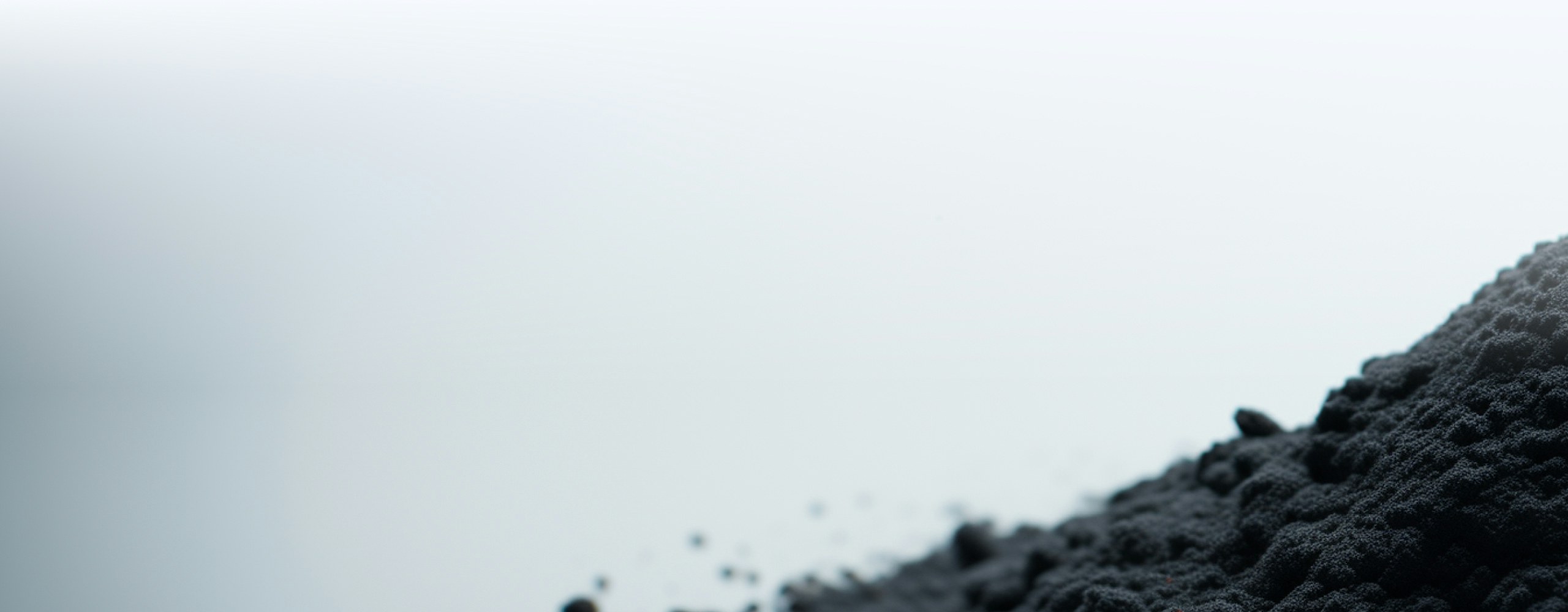
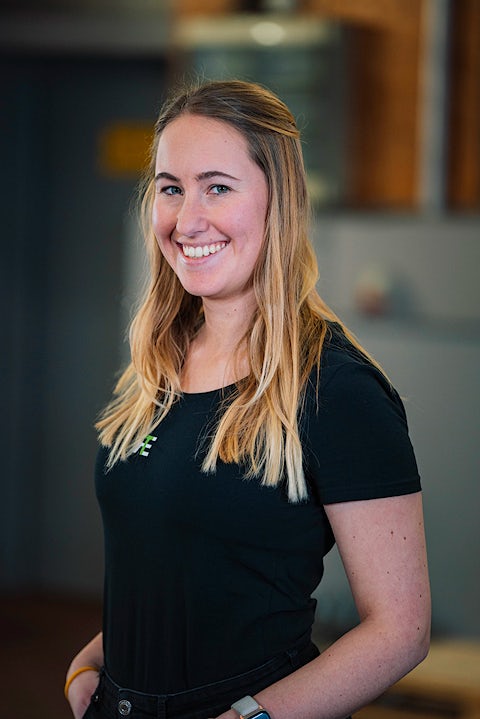
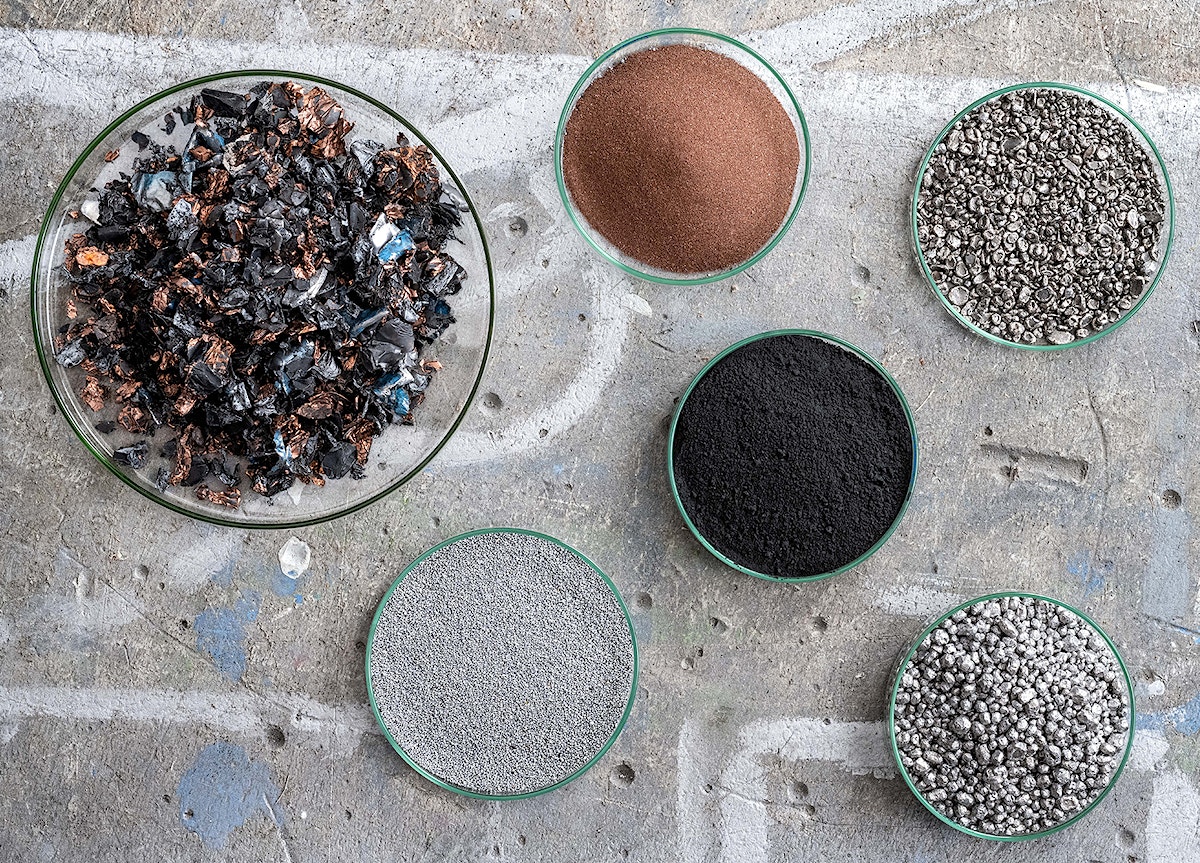
RECYCLING PLANT OPTIMIZES MATERIAL RECOVERY
What the Impact Reactor does in practice
A leading recycling company in Northern Europe uses the impact reactor as a crucial step in its battery recycling process. The aim is to separate pre-treated battery material efficiently and safely in order to recover valuable materials and prepare them for further processing.
Facts about the Case
The integration of recycled battery materials into electric vehicle production helps to reduce the amount of waste and promote a more sustainable circular economy in the automotive industry.
By using recycled materials, electric vehicle manufacturers can significantly reduce their carbon footprint.
The recycling process is already capable of recovering at least 95% of a lithium-ion battery - including valuable metals such as nickel, cobalt and lithium.
The battery recycling center has a capacity of approx. 10,000 tons per year. This is roughly equivalent to 30,000 batteries from electric vehicles.
Other Technologies
Revolution in battery recycling
From discharging and drying to separation in the impact reactor. All current lithium-ion batteries can be recycled safely and effectively in an efficient, clean process using state-of-the-art technologies.