Prallreaktor: Spitzenreiter fürs Batterierecycling
Mit unserem patentierten Prallreaktorsystem revolutionieren wir die Technik hinter effektiven Batterie-Recycling-Prozessen. Entdecken Sie eine der innovativsten Technologien weltweit für die Rückgewinnung von Black Mass in höchster Output-Qualität.
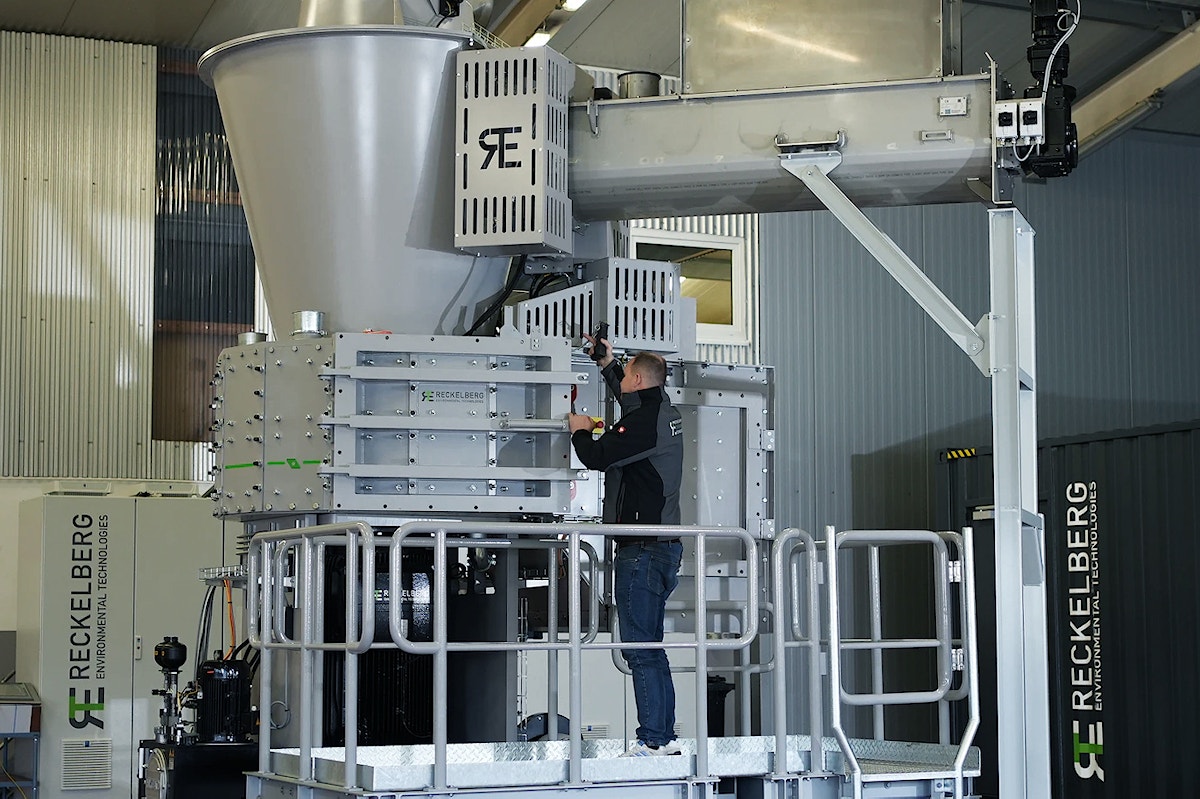
Mechanische SEPARATION von Rohstoffen
Der Schlüssel zur Revolution des Batterierecyclings
Für höchste Output-Qualitäten, unabhängig vom Inputmaterial.
Reckelberg Environmental Technologies revolutioniert das Batterierecycling mit dem Prallreaktor, einer zukunftsweisenden Technologie, die erstklassige Effizienz und Nachhaltigkeit bietet. Der Prallreaktor überzeugt durch seine Fähigkeit, Batteriekomponenten präzise zu trennen und wertvolle Metalle effektiv zurückzugewinnen. Er zeichnet sich durch eine hohe Materialreinheit und Ausbeute aus und ist zudem robust gegenüber Störstoffen. Für Unternehmen, die Wert auf Qualität, Effizienz und Nachhaltigkeit legen, bietet der Prallreaktor eine konkurrenzlose Lösung im Batterierecycling .
Highlights
Höchste Reinheit und Qualität der zurückgewonnenen Black Mass
Höchste Ausbeute wertvoller Metallfraktionen
Integrierte Abtrennung pulverförmiger Gefahrstoffe und robuste Konstruktion
Durch Geometrie des Prallreaktors besonders störstoffunempfindlich
Präzise Mechanik im Prallraum
Der Prallreaktor von Reckelberg Environmental Technologies nutzt eine fortschrittliche mechanische Verfahrenstechnik - speziell für das Batterierecycling entwickelt. Die effektive Trennung von Metallen und Black Mass im Prallraum, unterstützt durch hochverschleißfeste Prallelemente, stellt einen Schlüsselvorteil dieser Technologie dar. Konkret, beschleunigt ein spezieller Rotor das Material gegen die Wände, was unter Ausnutzung der Prallenergie des Materials untereinander und gegen die hochverschleißfeste Auskleidung des Prallraums zur Zersetzung führt. Das befreit schwere Gehäuseteile (Stahl und Aluminium) und Elektrodenmaterial (Aluminium und Kupfer) von der Black Mass und sorgt größtenteils für die Verkugelung.
Optimierter Luftstrom für maximale Trennung
Ein innovatives Luftstromsystem im Prallreaktor trägt zur präzisen Trennung von Materialien bei. Die Entschichtung der Metallfolien erfolgt innerhalb der ersten Sekunden und ein starker Luftstrom entfernt die freiwerdende Black Mass direkt aus dem Prallraum. Dies stellt sicher, dass keine Black Mass innerhalb von Metallkugeln eingeschlossen wird. Dieser Luftstrom entsteht zum einen durch die Bewegung des Rotors, zum anderen haben wir ein Spülluft- und Absaugsystem entwickelt, um die Black Mass nach oben zu befördern. Aufgrund des geringen Gewichts erfasst es auch Separatorfolien und kleinere Aluminium- und Kupferpartikel. Um diese Folien und Metalle aus der Black Mass zu entfernen, verfügt der Prallreaktor über Abweiseräder. Durch eine entsprechende Geometrie und Rotationsgeschwindigkeit dieser Abweiserräder erfolgt eine exakte Trennung zwischen staubender Black Mass und den „Störstoffen“. Das garantiert die hohe Reinheit und Qualität der zurückgewonnenen Black Mass.
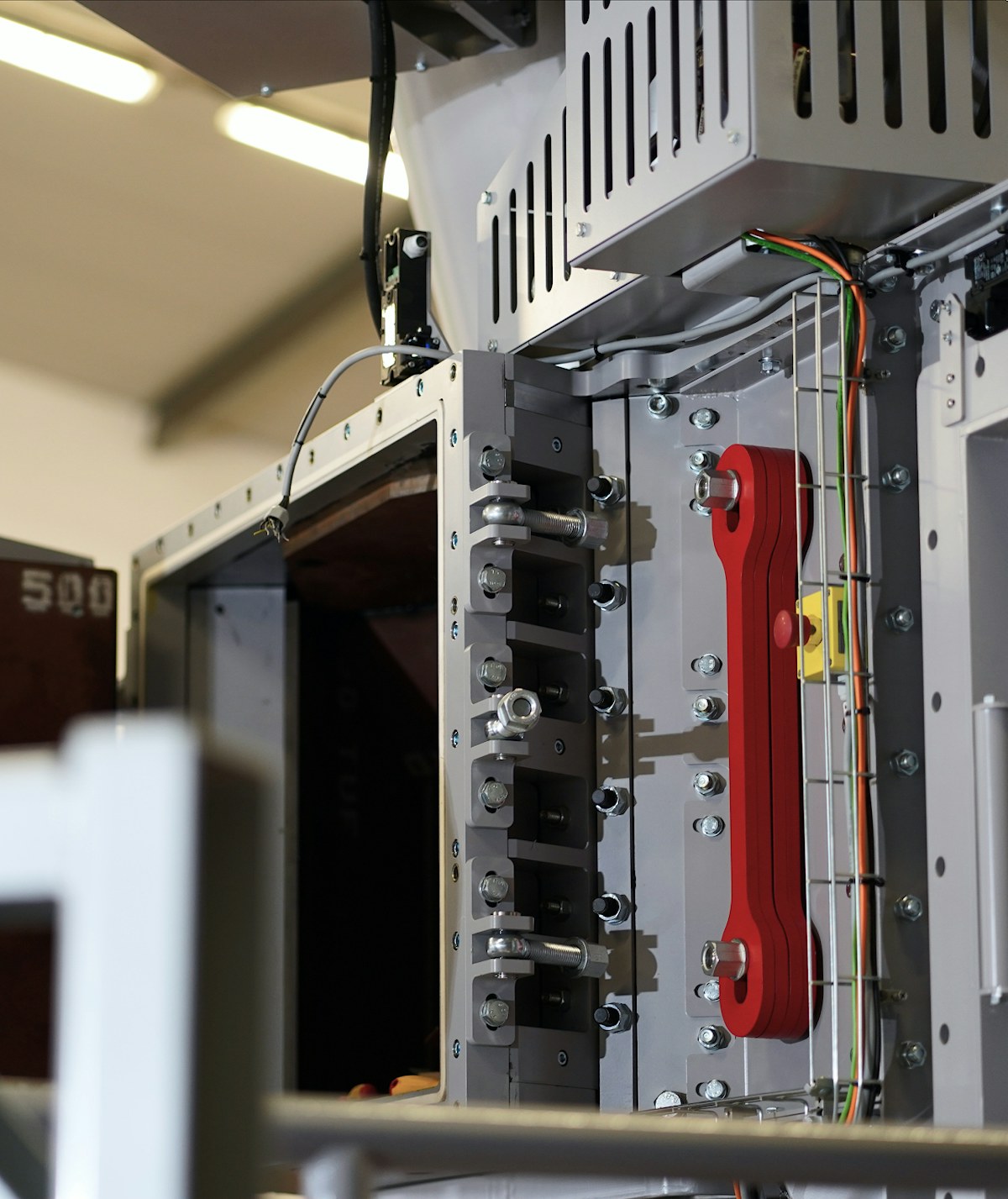
Effizienz und Nachhaltigkeit im Fokus
Der gesamte Prozess erfolgt in Batches bzw. Chargen. Nach Beenden einer Batch-Zeit, wird das verbleibende, von Black Mass gesäuberte, grobe Material über die Austragsklappe ausgeworfen und kann anschließend weiter separiert werden. Die Batch-Verarbeitung im Prallreaktor ermöglicht eine kontinuierliche und effiziente Materialtrennung. Der Prallreaktor ist mit seinem patentierten System und der überdurchschnittlichen Leistung der Garant für Effizienz im Recyclingprozess. Neben dem Recycling von Batterien eignet er sich auch für die CFK-Aufbereitung (Trennung der Carbonfasern von der Matrix), das Entschichten von lackiertem Holz und die Trennung von Kunstoff (PE)/Weißblech /Lack.
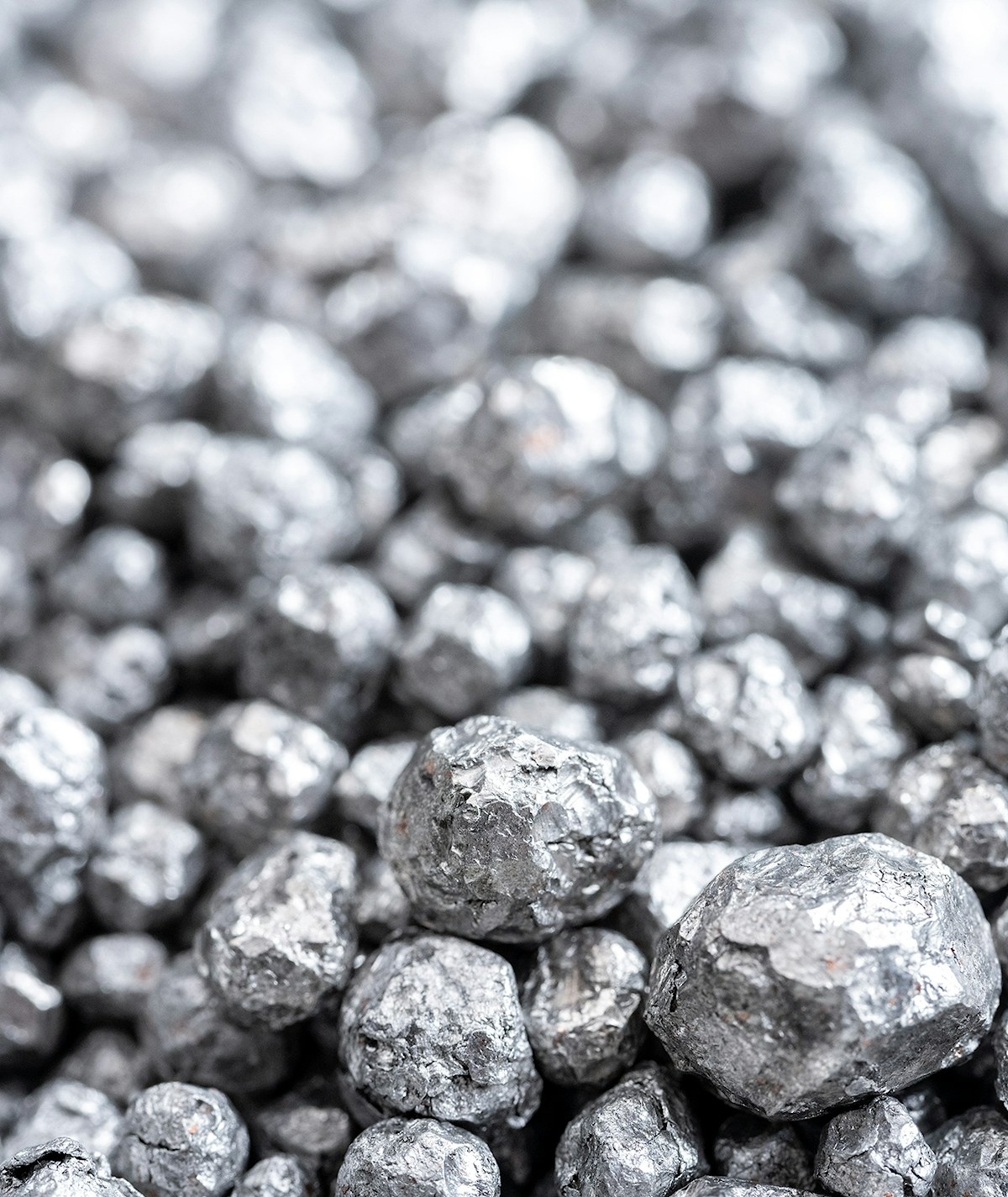
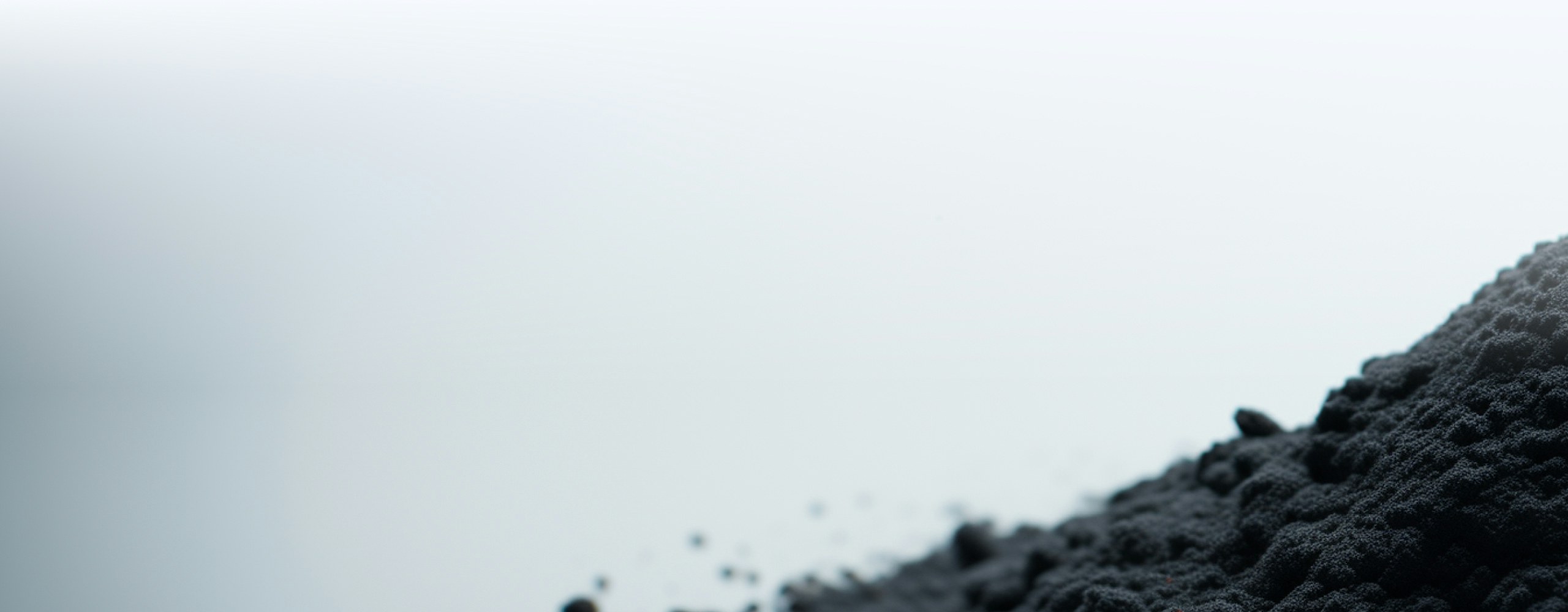
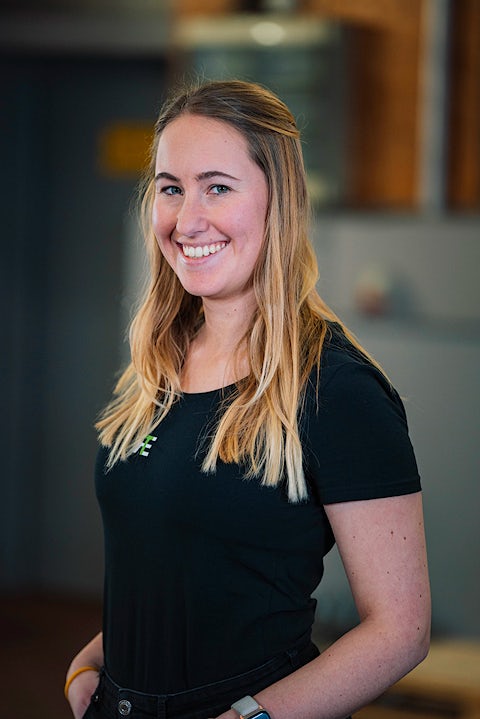
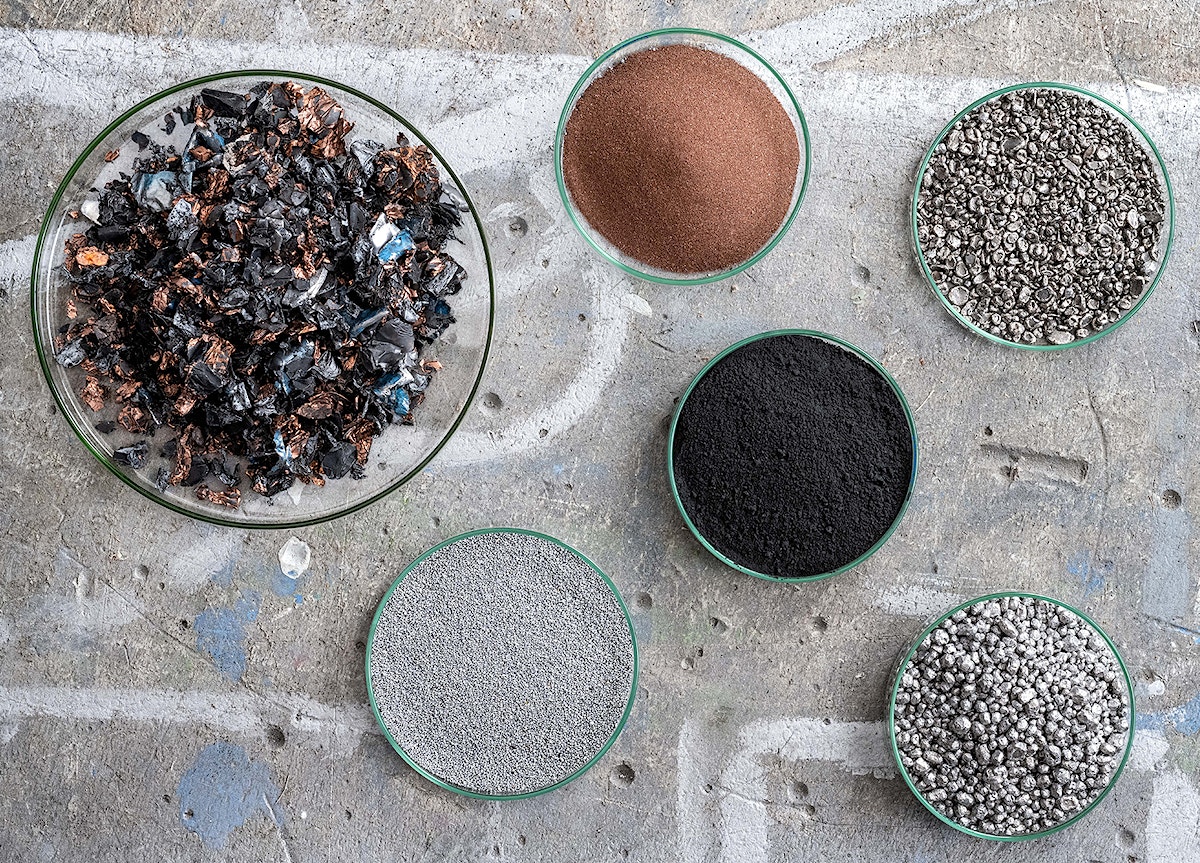
Recyclingbetrieb optimiert Materialrückgewinnung
Das leistet der Impact Reactor in der Praxis
Ein führender Recyclingbetrieb in Nordeuropa nutzt den Prallreaktor als entscheidenden Schritt in seinem Batterierecyclingprozess. Das Ziel ist es, vorbehandeltes Batteriematerial effizient und sicher aufzutrennen, um wertvolle Materialien zurückzugewinnen und sie für die Weiterverarbeitung vorzubereiten.
Fakten zu dem Case
Die Integration von recycelten Batteriematerialien in die Elektrofahrzeugproduktion trägt dazu bei, die Abfallmenge zu reduzieren und eine nachhaltigere Kreislaufwirtschaft in der Automobilindustrie zu fördern.
Durch die Verwendung von recycelten Materialien können Elektrofahrzeughersteller ihren CO2-Fußabdruck erheblich reduzieren.
Der Recyclinprozess ist bereits heute in der Lage mindestens 95% einer Lithium-Ionen-Batterie zurückzugewinnen - einschließlich wertvoller Metalle wie Nickel, Kobalt und Lithium.
Das Batterie-Recycling-Zentrum hat eine Kapazität von ca. 10.000 Tonnen pro Jahr. Das entspricht ungefähr der Menge von 30.000 Batterien aus Elektrofahrzeugen.
Weitere Technologien
Revolution in Battery Recycling
Von der Entladung, über die Trocknung bishin zur Trennung im Prallreaktor. In einem effizienten, sauberen Prozess mit modernsten Technologien können alle derzeitigen Lithium-Ionen-Batterien sicher und wirkungsvoll recycelt werden.